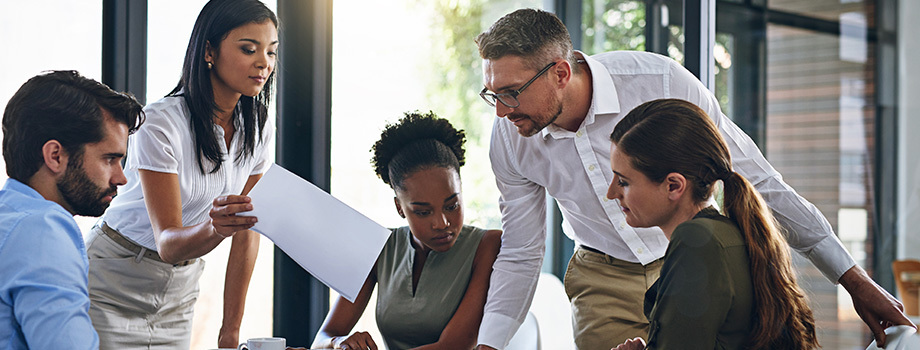
Projects in nearly any industry can benefit from capacity planning, which is a way of effectively coordinating who or what is available. In project management, capacity planning tracks people, skills, availability, and other resources such as space or equipment. It leads to the following benefits.
- Maximizes utilization to get more done with the same amount of people and resources.
- Secures real-time data on team availability, which increases the chance of on-time delivery.
- Enhances planning that takes into account the demand for resources and plans for it.
- Protects the team, avoiding task clashes and burnout.
- Organizes time to know what’s coming up and prioritizes what’s important.
Capacity planning is also applied to manufacturing. In this case, capacity planning concentrates on the efficient use of resources by examining the actual production of items.
The following sections approach the terms and methods found in incapacity planning. A capacity planning template is also provided.
Resource Capacity Planning Terms
Calculating capacity can be a simple process. To help streamline the capacity calculations, a number of factors must be considered by different stakeholders in the project. These include:
- Capacity: Capacity refers to the maximum amount that something can contain.
- Bottleneck: The bottleneck is the weakest link in a flow diagram. It represents the step that has the longest processing time.
- Process Capacity: This figure is equivalent to the capacity of the bottleneck, and can be used to calculate numbers like customers per hour or parts per day.
- Flow Rate: The minimum of demand and process capacity. It cannot be higher than the capacity of the bottleneck, but it can be lower if the demand is insufficient.
- Utilization: Utilization refers to how well a resource is being used.
Calculating capacity can be simple. A LinkedIn article provides a simple way to calculate the daily production capacity of a factory. Someone would need to multiply the total number of machines (200) by shift hours per day (10), which means that the total factory capacity in hours would be 2,000 hours.
Calculations can become complicated when other relevant information is provided. For instance, to calculate the number of standard minutes it takes to produce products, someone would need to work in the number of minutes it takes to produce certain products or the average for all products (25 minutes). Efficiency is also needed (50 percent).
The full formula is “Production capacity (in pieces) = (Capacity in hours*60/product SAM)*line efficiency,” which becomes “(2000*60/25)*50% pieces” or 2,400 pieces.
Methods of Capacity Planning
Aggregate Planning
Aggregate planning balances long-term strategic planning with short-term production success. This is a quantitative approach that uses projections to back up an operations plan. It requires inputs such as an aggregate demand forecast for the relevant period, an evaluation of the means to manage capacity planning (like sub-contracting and outsourcing), and the existing operational status of the workforce, inventory level, and production efficiency.
There are three types of aggregate planning strategies – level, chase, and hybrid. The level strategy maintains a steady production rate and workforce level, resulting in a steady workforce but leading to high inventory and increasing backlogs. Chase’s strategy dynamically matches demand with production, lowing inventory levels, and backlogs, but lowering productivity, quality, and the workforce. The hybrid strategy balances level strategy and chase strategy.
Theory of Constraints (TOC)
The Theory of Constraints (TOC) improves profitability by identifying a bottleneck in the process that impedes a plan. It’s “a methodology for identifying the most important limiting factor (i.e., constraint) that stands in the way of achieving a goal and then systematically improving that constraint until it is no longer the limiting factor,” according to production monitoring and performance management system company Vorne. “In manufacturing, the constraint is often referred to as a bottleneck.”
The TOC takes a scientific approach to improvement that tries to make a profit, both in the short term and in the long term. There are powerful sets of tools that go along with the TOC, in an effort to achieve that goal.
- The Five Focusing Steps: This is a methodology for identifying and eliminating constraints. The steps are: identify the current constraint; make quick improvements to the throughput of the constraint using existing resources; review all other activities in the process to ensure they align with and support the needs of the constraint; if the constraint still remains, consider further actions to eliminate it from being the constraint (e.g., the capital investment may be required); immediately address the next constraint to continue through the improvement cycle.
- The Thinking Processes: This includes tools for analyzing and resolving problems, including current reality trees, evaporating cloud trees, future reality trees and strategy, and tactics trees. The Thinking Processes are used to answer three questions integral to TOC. What needs to be changed? What should it be changed to? What actions will cause the change?
- Throughput Accounting: This is a method for measuring performance and guiding management decisions. It seeks to eliminate traditional accounting practices that promote behaviors contrary to the goal of increasing profit, such as believing that inventory is an asset. “This often drives undesirable behavior at companies – manufacturing items that are not truly needed,” according to Vorne. “Accumulating inventory inflates assets and generates a ‘paper profit’ based on inventory that may or may not ever be sold (e.g., due to obsolescence) and that incurs cost as it sits in storage. The Theory of Constraints, on the other hand, considers inventory to be a liability – inventory ties up cash that could be used more productively elsewhere.”
Incremental Capacity Planning
Forward incremental planning (FIP) is implemented when a receipt for an order is received and prioritizes actions required to fulfill that order. It attempts to reduce lag time. This approach is ideal for companies that produce products with high amounts of customization, as FIP assumes no other actions are in process (machines aren’t tied up and the workforce is idle).
Backward incremental planning (BIP) reverses FIP, examining the requirements from the due date backward and organizing the process accordingly. It works well when deadlines have requested completion dates and fulfilling orders early produces no benefit (such as at a bakery).
Pursuing a Career in Business
Aurora University’s online bachelor’s in business administration and online MBA help students develop the knowledge and skills needed to advance their careers. Students receive instruction in current business practices from faculty members with real-world experience. Each program takes place in a fully online learning environment.